Contents
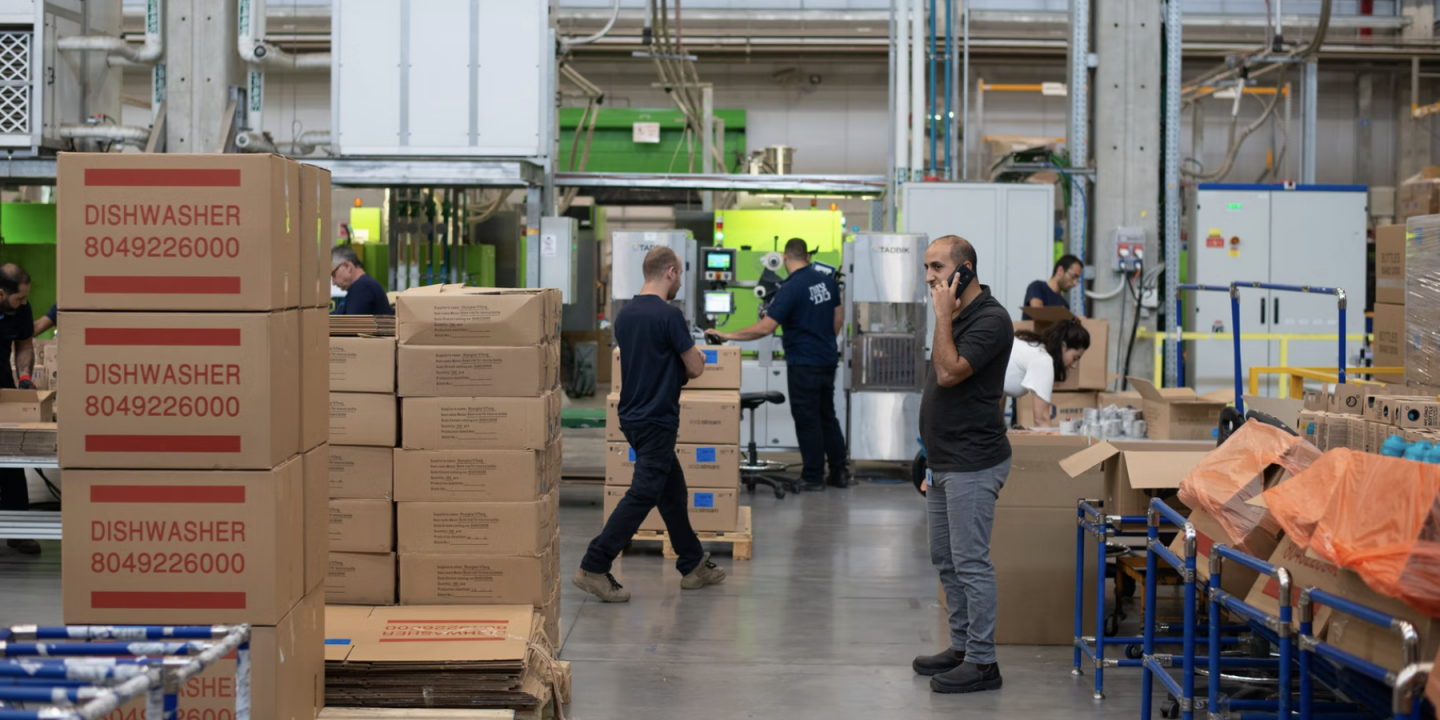
Warehouse picking is the process by which items are picked in a warehouse to fulfill customer orders. This is often the basis of a positive order fulfillment process.
Warehouse picking is a process that must be done accurately and efficiently. If it’s not, items are missing from orders or customers get the wrong items. Poor practices can also result in wasted time, more labor costs, and decreased customer satisfaction levels.
In today’s technological world, warehouse picking can be improved with warehouse management systems and robotics. By implementing improved picking strategies, companies can save time and money, improve efficiency, and increase their bottom line in the process.
What Is Warehouse Picking?
Warehouse picking involves pulling items to fulfill customer orders. Essentially, the items listed in an order are picked from the warehouse and grouped to be sent to the customer. Picking is the first step in the physical order fulfillment process, and it must be done accurately to ensure the rest of the fulfillment process (packaging and shipping) can run smoothly.
Order picking costs companies a lot of money. The costs involved in finding items and picking them for orders can make up a big portion of labor costs. By streamlining warehousing picking processes, companies can save a lot of money in the long run.
It’s incredibly important that warehouse picking is done accurately. If orders are not fulfilled correctly — whether items are missing from an order or the wrong items are included — this can have a devastating financial impact on companies in the aggregate. Customer satisfaction rates will eventually plummet if order fulfillment is an ongoing issue.
Types of Warehouse Picking
Different warehouse picking strategies will work better for certain companies, but the key is to identify processes and strategies that will work well for your warehouse. The right strategy for you will depend on things like the number of different types of products in your warehouse, the size of those products, the number of employees working at one time, and your overall organizational setup.
Here are some of the most popular types of warehouse picking approaches:
Discrete Picking
This type of picking tends to work best for small e-commerce retailers with somewhat limited inventories. It involves one picker working on a single order at one time. They simply retrieve all the items in the order based on SKUs.
This method of picking involves a lot of back and forth movement as the picker gets each item for the order. Since a picker fully completes one order before moving on to the next, they never gather multiple quantities of a product to fulfill multiple orders at once.
The primary benefit of discrete picking is a high level of accuracy in order fulfillment. Since the process tends to be slower, pickers make fewer errors, but each order eats up a lot of time.
Batch Picking
With this method, pickers work on multiple orders at one time. In some warehouses, batching picking is used in combination with discrete picking. With batch picking, pickers are able to travel a bit less since they can grab items from one area of the warehouse that will be placed in multiple orders.
Zone Picking
If a warehouse is large and split into different zones, this method of picking is frequently used. Pickers are assigned to specific zones, and they only pick from that zone.
This is sometimes called the pick-and-pass picking method since it works similarly to an assembly line. A single packer knows their zone very well, so they are able to quickly pick the items. This means the entire process moves faster since each picker is an expert in their zone.
Zone picking works particularly well when warehouse slotting is also used to organize the warehouse most efficiently. Items with high turnover should be kept in one zone whereas items with low turnover should be kept in another zone. High-turnover zones may require multiple pickers, depending on volume.
Wave Picking
This type of picking involves order consolidation. Orders are assessed to determine when waves of items should be picked. Then, all items in that wave are picked together. They are then sent to a consolidation area where they are sorted into individual customer orders.
Wave picking is typically used by large operations that have high-volume orders. It allows the picking process to move much faster since all the items in a wave are picked at once without concern for sorting. The sorting happens in the consolidation area before orders are packed. Orders are prioritized by importance and shipping times.
How Can Technology Improve Warehouse Picking?
While warehouse picking strategies can all be done manually, technology can greatly simplify the process. In the past, pickers used pick lists where all the items to pick were listed on a sheet of paper. Today, automated picking systems act as a pick list.
These systems don’t just list the items that need to be picked. They suggest the best routes to the item location and confirm accuracy. If the SKU on a product doesn’t match the pick list, it notifies the picker, helping to cut down on errors in the picking process.
With the right technology and improved picking processes, customers enjoy a streamlined and accurate fulfillment process. They are less likely to receive incorrect orders, and this means they are more likely to purchase from you again in the future. They’ll also receive their orders sooner since the picking process is quicker.
Your employees will be happier when efficiency improves in the warehouse picking process. No one wants to feel like they are wasting time walking back and forth across the warehouse when there’s a better way. They’ll accomplish more in a work shift, which is good for employee morale and your bottom line.
Best Practices for Warehouse Picking
Consider these best practices to improve your warehouse picking strategies:
Invest in warehouse slotting.
By organizing your warehouse well via process called warehouse slotting, you’ll save time and money. Workers won’t have to travel as far for high-demand items, orders will be fulfilled faster, and storage can be reduced.
Consider a warehouse management system.
Let technology do some of the heavy lifting for you. Automated processes can show you ways to maximize your storage space, improve picking routes, and boost order fulfillment accuracy. You’ll know when to stock inventory that’s low, helping you to reduce hiccups in the fulfillment process.
Ensure you have the right picking equipment.
If pickers don’t have the right equipment to pick, it’ll slow everything down and also put them at risk. Assess your picking equipment inventory, and consider whether you have sufficient forklifts, stack pallets, barcode scanners, and handheld or wearable tracking devices. These things can all improve efficiency and reduce errors.
Consider new technologies.
Robots are frequently used in the picking process in today’s warehouses. Robotic technology allows robots to navigate warehouses quickly via magnetic strips and to pick quickly using inventory data, such as product SKUs, location information, sensors, and cameras.
Voice picking equipment is another newer technology you can implement in your warehouse. This involves vocal prompts for order picking. Generally, a headset is connected to a mobile device, and the picker is given verbal directions on where to go and what to pick.
Which Warehouse Picking Strategy Is Right for Your Business?
With so many different strategies available, it can be tough to know which one is right for you. Consider the big picture in terms of your product inventory, order volume, warehouse space, and seasonal trends. Use the data you gather to make an informed decision on the best picking practices that will work for your business.
Make sure to track productivity levels to determine if the approach you’ve chosen is working or can be improved. It will often save you time and money to work with a third-party logistics management company that can help you analyze your warehouse data and devise warehouse picking strategies that will work best.
References
A Retailer Increases Warehouse Picking Productivity by 50% With Automation. (May 2021). Forbes.
What’s Driving the Need for Robots in Warehouses? (July 2021). Forbes.
The Robots That Are Running Our Warehouses. (May 2021). CNN.