Contents
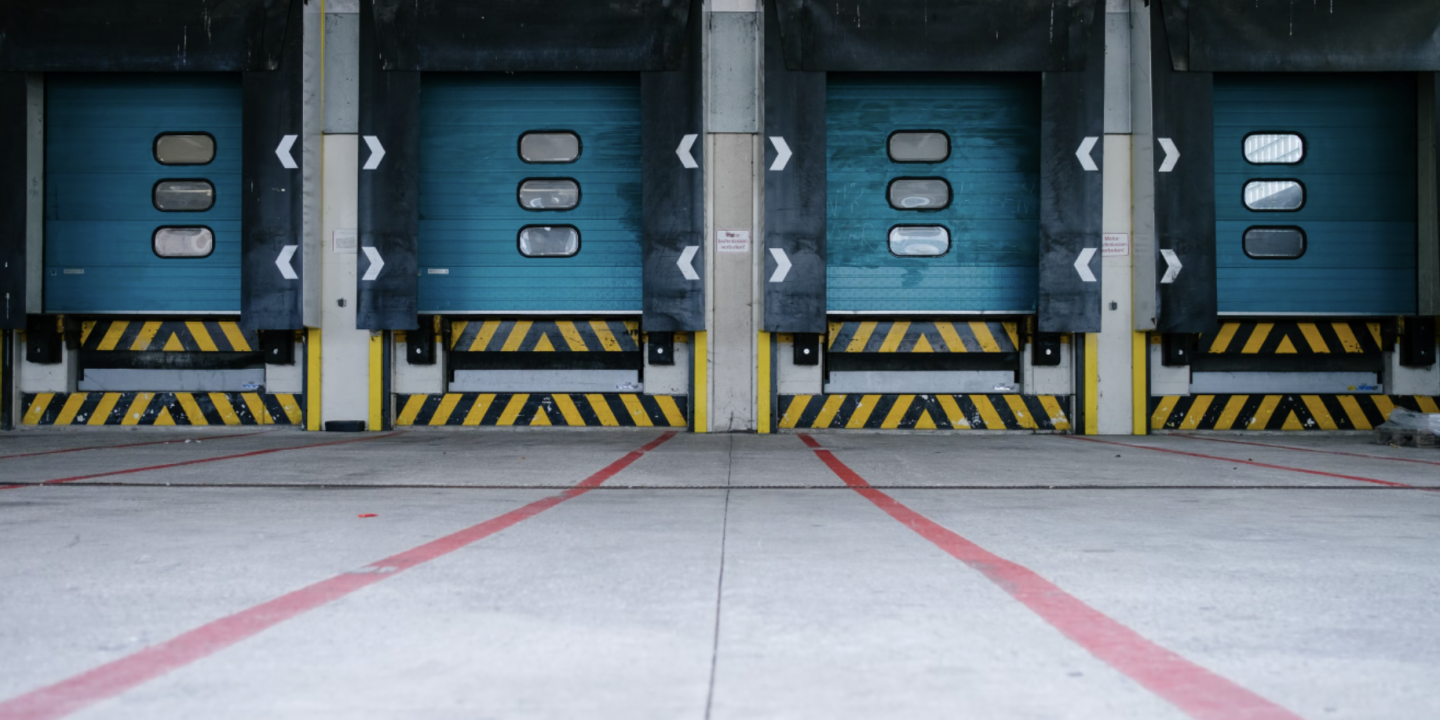
Cross-docking essentially removes the storage aspect of transporting goods. Whereas goods are normally moved from a mode of transportation to a warehouse or other storage facility, cross-docking moves the product directly to the customer or another transportation option immediately.
What Is Cross-Docking?
In a nutshell, cross-docking simplifies the distribution process for goods. Storage is taken out of the equation or minimized as much as possible. This enables significant savings on storage costs.
With cross-docking, products arrive on shipping containers or trucks. They are immediately unloaded, sorted, and then loaded onto outbound trucks or railroad cars to continue to their destination.
What Are the Benefits of Cross-Docking?
Cross-docking has a number of benefits for both businesses and consumers.
- Cost savings: It essentially removes the intermediary step of sitting in a warehouse. Without cross-docking, items would be unloaded from the initial truck or container, put into a warehouse, reloaded into the next truck or container, and then continue to their final destination.
In addition to warehouse fees, business owners also have to bear the added labor costs of unloading and reloading the goods an additional time. Cross-docking saves those costs.
- Time savings: With a more streamlined inventory management system, cross-docking can save companies a substantial amount of time. Because goods are put in vehicles shortly after arrival, they don’t need to be scanned into a warehouse management system where they are stored. It essentially removes a couple of steps in the distribution process, helping to remove unnecessary work and reduce labor costs in the process.
- Faster shipping times: Because goods aren’t stored in a warehouse, they reach customers much sooner. When large inbound batches come in, they are broken down and organized into smaller batches that are traveling in the same direction. This leads to much better transportation and shipping competence, helping customers to ultimately get their goods sooner.
- Enables higher inventory turnover: With cross-docking, goods need to be handled less. When you have a cross-docking inventory system, it isn’t as extensive as a warehouse management system, and there are fewer steps involved. You don’t have to track your goods as extensively since inbound goods quickly become outbound.
- Less wear and tear: When products are handled less, their quality is improved. This is particularly true for perishables like food products. The less they are handled, the better. With less inventory handling, there is a reduction in the potential for damage to goods.
What Is Needed for Cross-Docking?
With clear benefits of cost savings and efficiency, it seems that every business should be doing cross-docking. But it does require a good amount of planning and organization to do it well. This is often why some businesses don’t attempt this approach.
In order to do cross-docking well, there needs to be a cross-docking terminal between inbound and outbound trucks or transit. This is an area where workers can unload the goods from inbound trucks, sort them accordingly, and load them into outbound trucks.
Types of Cross-Docking
There are two primary types of cross-docking.
- Pre-distribution cross-docking: This type is normally used when the end customer is known prior to shipping the merchandise. Essentially, the customer and shipping address are known before the merchandise leaves the supplier. Pre-distribution cross-docking works best for e-commerce retailers that manage all their customer and supplier relationships.
- Post-distribution cross-docking: With this method, goods are stored at the cross-docking facility until the end customers are identified. While some storage is involved, this gives the supplier time to make informed and wise choices about how the goods are distributed. With this method, retailers are able to optimize how goods are shipped based on inventory predictions.
Different Ways to Cross-Dock
There are three primary methods used to cross-dock.
- Continuous cross-docking: This is what most people think of when cross-docking is referenced. Products continually move through a cross-docking terminal or facility, moving goods from inbound to outbound shipments. Goods generally move quickly with very minimal storage time, if any. If goods do wait at the facility, it is usually only due to timing issues with inbound and outbound trucks or shipments.
- Consolidation: This method involves combining smaller freight loads into a single larger load. The idea is to save shipping costs by merging smaller loads that are all headed in the same direction. There does need to be sufficient storage space for goods while smaller loads are gathered.
- Deconsolidation: This is the opposite of consolidation. It involves breaking down a large freight load into smaller loads to allow for easier transport. Often, this method is used when the inbound load will be broken down and shipped directly out to consumers.
Is Cross-Docking Right for Your Business?
Cross-docking can benefit any business that is looking to reduce storage and labor costs and improve shipping times and efficiency.
It works particularly well for companies that have time-sensitive products like perishable goods. These goods can’t sit on warehouse shelves. They need to quickly move out so they get into consumers’ hands faster.
Cross-docking is also a good choice for e-commerce retailers that use multiple suppliers. Retailers can gather inbound goods from various supplies, quickly sort them, and then send them outbound to consumers. They won’t have to spend money on storing the goods unnecessarily.
Whatever your business model, cross-docking can streamline the order fulfillment process, particularly for bulk shipments. If your business has consistent, steady demand, cross-docking just makes a lot of sense. Your product will move more quickly, and your customers will be happy to get their orders sooner.